Why Manufacturers’ IIoT Strategies Fail – and How Yours Can Succeed
Plenty of ink, digital and otherwise, has been devoted to the topic of the Industrial Internet of Things (IIoT) and the benefits it has in store for manufacturers who pursue it. For an alarmingly high number of companies, those benefits have failed to become reality. In fact, according to Cisco, only 26% of IIoT strategies are deemed a complete success by those who devised them. The rest linger somewhere between works-in-progress and outright disappointments. Despite those numbers, IIoT is more than a mere buzzword or marketing fluff. It’s an investment that can generate game-changing outcomes for those manufacturers prepared to take it on.
Where IIoT strategies go off the rails
So, what’s holding manufacturers back from writing their own IIoT success stories? There’s no simple answer. For many, issues rear up during the pilot phase. One study, conducted by McKinsey and Co., found 84% of IIoT projects get trapped in pilot mode for more than a year. These early stage struggles echo in the Cisco study mentioned above. It found 60% of projects seen as anything other than a total success shut down before advancing out of the proof of concept phase. Part of this inability to move forward may stem from an abundance, or even an overabundance, of caution. It may also be a symptom of a bigger and all-too-common issue.
Instead of seeking out IIoT for help with a specific obstacle or need, we’ve seen manufacturers chase it for a different reason. Given IIoT’s widespread popularity and position alongside other white hot topics like artificial intelligence, some companies have pursued it solely for fear of falling behind. The thing is, successful IIoT implementations must begin with a clearly-defined target, something like reducing scrap by a given percentage, in mind. Without a set objective to guide the way, it’s clear why so many projects sputter out early on.
Uncertainty in terms of destination is a problem but so too is a lack of familiarity with the solution itself. Even if they know exactly what they want to achieve with IIoT, manufacturers will struggle to realize its upsides if they don’t have experience with the technologies that define it. That lack of experience can also surface on the project management side. Smart solution implementations are complex, often multi-faceted engagements. Organizations who’ve never gone through one of those projects before can easily become overwhelmed or under estimate their needs. In either case, the consequences can be serious.
Another major reason IIoT strategies go astray? Smart technologies don’t fit nicely within siloes. By their very nature, they span multiple departments and levels. IIoT strategies that maintain a narrow focus are limited in what they can achieve and may face sharp pushback should they attempt to expand later. Unfortunately, too many manufacturers’ C-Suite leadership prefers to take a hands-off approach to these types of strategies. This sends a dangerous message down the chain of command about the importance of IIoT. Further, without their leadership, critical cross-functional thinking may fail to take hold.
How to keep IIoT strategies moving forward
IIoT strategies can hit snags but so can any other improvement project. Focusing on these three areas and incorporating the following best practices can help manufacturers join the growing ranks of IIoT success stories.
- Formulating a winning strategy
Before anything else, it’s important to anchor a strategy in real world data. By answering these self-assessment questions – with help from across departments and organizational levels – manufacturers will be able to trust that their IIoT strategies are heading in the right direction.
– “What does IIoT success look like for me?” As discussed above – start with the destination in mind. Know the objectives and then architect the technical environment needed to achieve them.
– “How will I know when I’ve succeeded?” Before a project begins, measure. Stakeholders must appreciate the state of an environment pre-IIoT. After the project has wrapped, measure again. This data will prove whether a project was a success or if it needs to be revisited.
– “Am I biting off more than I can chew?” IIoT can make a sweeping difference for businesses, but it can’t happen all at once. Prioritize desired outcomes and use them to inform a long term, gradual approach to IIoT implementation.
– “Do I have the expertise to pull this off?” As mentioned, IIoT projects are complex, jammed with moving parts and variables. If there isn’t firsthand experience on staff with managing and executing this type of project, it would be wise to call in the help of a partner who’s been there before.
– “Am I collecting the right data?” IIoT can put a universe of information at a firm’s fingertips. While it is tempting to gather as much as possible, again, it comes down to prioritization. Determine the data sets that promise to be most actionable and have the biggest impact and start there.
- Shifting organizational culture
Above we mentioned how bridging the gap between departments is instrumental to IIoT success, but doing so is often easier said than done. Typically, groups such as IT exist in one world, tending to the infrastructure, hardware, software, etc.; while OT focuses on the devices and processes leveraged on the shop floor. IIoT must be the link that unites these groups.
Getting those two pieces of the manufacturing puzzle out of their silos and onto the same page starts with training. Set aside time to cross-train engineers from each side on what those on the other do, what they care about, and the rules that govern them. It’s only through hands on experience that IT and OT will ever truly widen their vision.
Still, it’s not just a matter of familiarizing one side with the other’s responsibilities, it’s about making them one and the same. Both sides should ensure IIoT “to do list” items account for each other’s needs. So, for example, routine outages should coincide with production downtime as closely as possible. In this way, neither side will see the other as an obstacle but rather as a necessary partner.
With the proper cultural foundation, engineers from each side can take on the multi-functional responsibilities of an IIoT deployment together, with each lending their particular discipline – operational, organizational, or technological.
- Building a strong technological base
Organizational culture isn’t the only thing IIoT may transform. Existing technological environments will find themselves handling a far heavier workload than they did previously. Everything from wireless architecture to security protocols will need to be rethought and revamped to manage the increased demand. Failure to make the appropriate changes may not just leave manufacturers struggling to achieve their desired ROI, it could leave them vulnerable to attack.
Here’s a high-level primer on prepping IT environments for IIoT:
– Conduct a facility assessment. Together, IT and OT personnel should create a rough portrait of their facility’s existing technological profile. Example: Compiling a list of the device types currently drawing on things like wireless, the bands on which they operate, and any possible sources of interference in areas where IIoT solutions will be deployed. All of this information can help prevent network bottlenecks or any other surprises later on.
– Thoroughly vet available replacements. Remember, best of breed doesn’t automatically mean best of fit. Instead of looking to the latest and greatest tools on the market, businesses would be better served reviewing their objectives and their constraints. Run all potential upgrades against the standard of “Is it the best for us?” instead of “Is it the best?”
– Have a support system in place. New technologies, whether they’re upgraded security solutions or even IIoT itself, mean new workloads. Manufacturers must ensure they have access to the skill sets needed to manage these new additions. If applicable, they must also have the resources in place to monitor and act on any data sets generated by these technologies.
– Allow room for future growth. Gartner predicts there will be 20 billion connected things by 2020. By that point, IIoT alone could be just shy of a trillion dollar industry. As IIoT investments continue to grow, manufacturers will want to leave themselves room to do so. That may involve re-architecting existing data center, networking or security solutions to provide a bit more bandwidth than initially needed.
Next steps: Where to turn for IIoT support
Succeeding with IIoT doesn’t have to come down to a roll of the dice. With the help of the right partner, manufacturers of all sizes and budgets will be able to count themselves among the businesses who’ve built a successful IIoT strategy. Want more insights into building and executing on a winning IIoT strategy? Reach out to Arraya Solutions today by visiting us at https://www.arrayasolutions.com//contact-us/.
Feel free to leave us a comment on this or any of our blogs through social media. Arraya can be found on LinkedIn, Twitter, and Facebook. Once you’ve let us know what you think, follow us to stay updated on our industry insights as well as our exclusive technology learning opportunities.
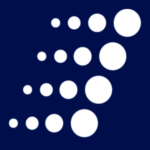